Condition Monitoring is becoming the mainstay for maintenance and reliability groups in virtually all industries; as such, there needs to be a system in place to demonstrate the effectiveness of the activities involved. While it is hard to argue the impact of detecting problems early, the question remains: how in-tune are we with our equipment? The best condition monitoring programs utilize metrics to answer this question along with others. What follows are are the top three condition monitoring Key Performance Indicators (KPIs) in no particular ranking.
Percent abnormal readings/measurements/results -
The key to good condition monitoring is to take routine measurements in the field. These may include oil or grease samples, vibration readings, ultrasonic inspections and myriad others. When we interpret these measurements, we should be looking to find the equipment that is in an “alarm” or “abnormal” state. By comparing the number of machines in this state compared to the total number of machines in the program, this percentage takes shape. Programs in their infancy are often inundated with the number of problem samples coming back, so this serves as a metric to show the evolution of the program over time as well as a leading indicator of unplanned downtime. While the goal is to have as low of a percentage as possible, it is likely that some percentage of equipment will be flagged for some reason, such as contamination, fluid health or machine health.
Issues found via in-person (non-instrument) inspections -
Much emphasis is put on the technology side of condition monitoring, but it’s important to remember the value of the daily inspection. This KPI is so important because it can be a shared metric across multiple departments within the facility. It is not uncommon for mechanics, operations and lube technicians to all have a set of daily routes and rounds that they have to accomplish at the beginning of their shifts. Since we have different sets of eyes on the equipment, we should be tracking the abnormalities or problems found during these events. Remember that what gets measured gets done; all too often, the inspections are pencil-whipped because no action is taken on problems reported or sheets are simply turned in and filed away, never to be reviewed. By having a dashboard or bulletin board indicating the number of “saves” found by the inspectors, you can promote a culture of equipment care across multiple sets of employees and help break the silos and constant struggle of maintenance against operations or any other conflict that seems to be present in facilities.
Effectiveness of corrective actions taken for equipment -
Finding problems early is the ultimate goal of condition monitoring, but we need to look beyond finding the issues and work to determine how well we are correcting the problems. This can be done based upon how long the equipment stays in an “alarm” state and, even better, can be crossed with the specific action taken to remediate the problem. Not only will this metric answer the question of “are we addressing the problems,” but it also serves as the beginning of a decision matrix that should be developed for each type of alarm that is triggered when the equipment develops issues. The matrix can be reviewed and makes the troubleshooting and correcting of the problem much simpler as opposed to just guessing at what may fix the issue. Obviously, good documentation is key to this one as the information recorded in the decision matrix will serve as the foundation for equipment corrective action in the future.
While there are many more metrics that could be measured and tied to specific condition monitoring activities, starting with the few key metrics will help narrow the focus of the program to exactly what we are trying to achieve.
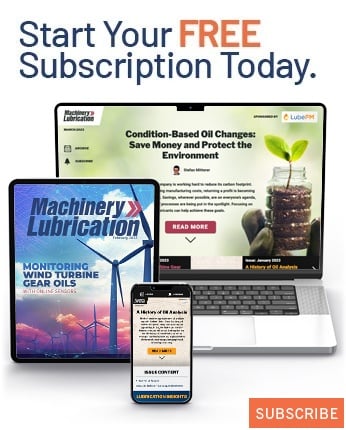